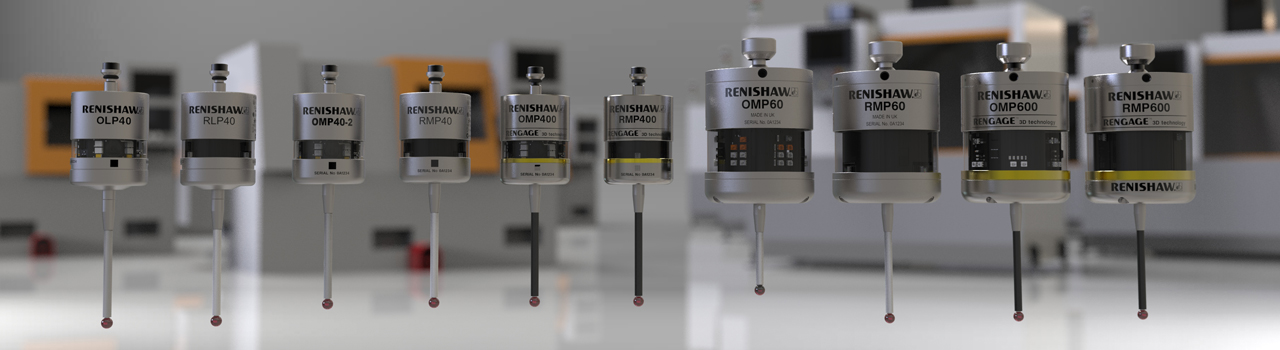
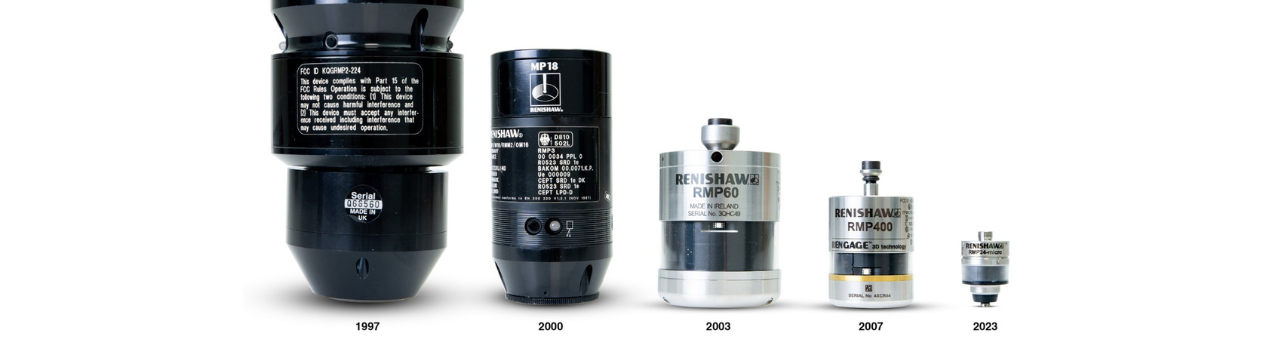
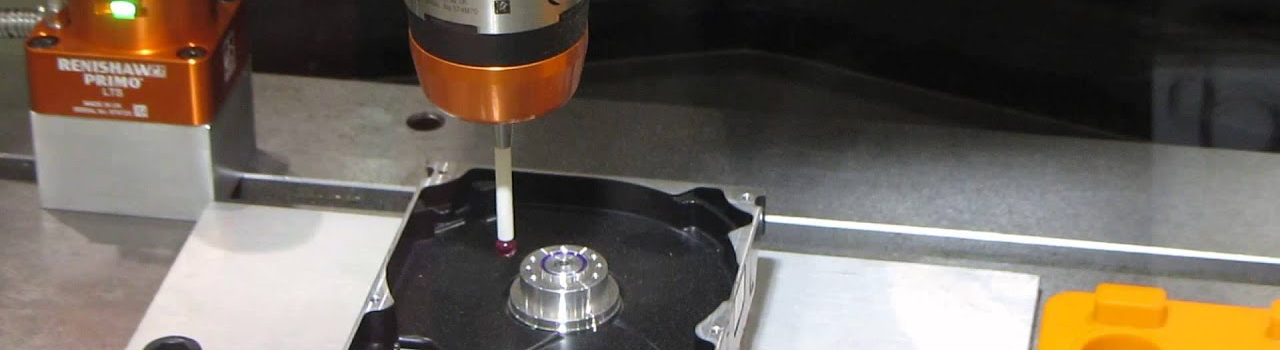
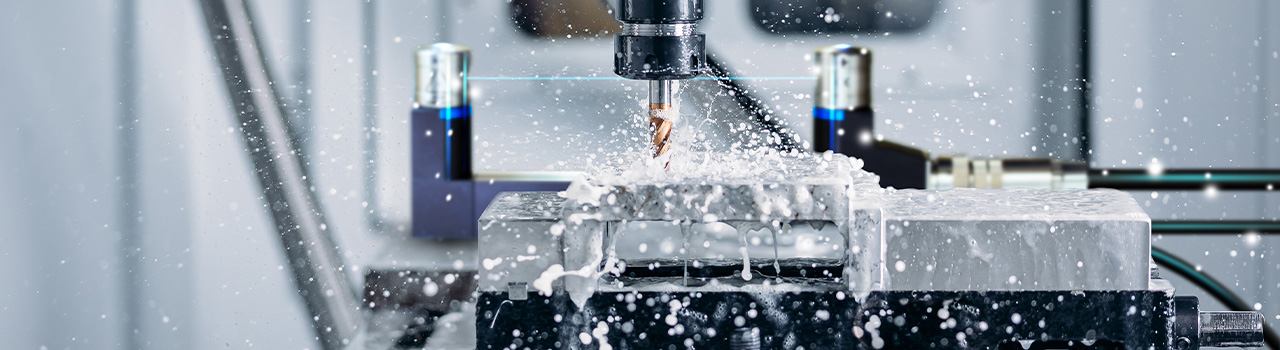
Procal Solution offers renishaw make a comprehensive range of probing and tool measurement systems for CNC machine tools. Designed to improve machining accuracy and efficiency, our automated systems deliver significant cost savings and quality improvements.
Machine tool probing and on-machine tool measurement is an established best practice in the machining industry. Manually setting and inspecting tools and parts can be detrimental to machining performance and profitability. Our probing and tool setting systems help manufacturers to reduce scrap rates, eliminate machine down-time, and improve component quality.
Our solutions enable automated component set-up, in-cycle gauging, tool setting, and broken tool detection. When coupled with automatic offset updates, our technology enables you to machine with confidence, reduce set‑up times, and improve process control.
Workpiece and tool measurement can happen before, during, and after machining tasks. By practicing this type of measurement, eliminate costly machine downtime and component scrapping. This allows you to better invest your time and money into productive machining.
An inaccurate machine cannot consistently make accurate parts. Regular machine tool maintenance and health check monitoring is essential for reliable, high-precision machining.
These types of preventative actions help to reduce sources of variation. They are the foundations of process control and ensure a consistent and efficient machining process.